Numerical flow simulations
Numerical flow simulations (CFD – Computational Fluid Dynamics) are usually accompanied with the development of burners, reactors, basic test rigs and evaporators. A significant field of application is to analyse the characteristics of fluids and thermodynamic processes during synthesis gas production in microstructures. As part of the project MÖWE I – III, which was publicly funded, numerical flow simulations of a heating-oil-steam-reformer were performed. The reactor is a catalytically coated micro heat exchanger in which the steam reforming process is heated by catalytic combustion situated in parallel. The CFD-simulation aims at the optimisation of the fuel conversion and the homogenisation of component temperatures.
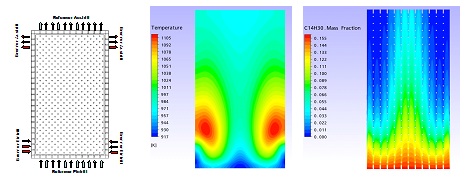
Heating-oil-steam-reformer MÖWE Project: temperature distribution in the reactor plate and the concentration distribution of the fuel in the reformer. Photo: OWI
One core competence of OWI is the development of premixing techniques for liquid fuels. Specifically, investigations related to the evaporation of diesel and heating oil drops in the air which are supported by fluid dynamic simulations. Evaporation models which are implemented as standard in commercial CFD-codes contain various simplifications. The thermodynamic properties of multi component fuels, such as heating oil, cannot be reproduced with sufficient precision. At OWI, a drop evaporation model based on the concept of continuous thermodynamics has been developed and implemented in the CFD software. The model was validated for single droplet and spray evaporation of heating oil by means of experimental data. The model can be used in particular for optimising mixture formation in burners.
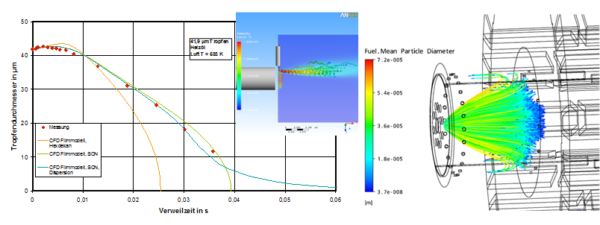
Validation oil drop evaporation and calculation of a recirculating burner (droplet paths). Photo: OWI