Thermoacoustic sensor technology
Development of thermoacoustic sensor technology for industrial furnaces to detect flame stability limits when using natural gas-hydrogen mixtures – contributions to flame diagnostics and noise reduction in furnace construction
Brief description
Furnaces are a major source of noise emissions in industrial plants. Combustion noise of turbulent flames cannot be suppressed. Noise emissions above this noise level may indicate combustion chamber pulsations or vibrations. The resulting reactions depend on a variety of geometric factors and operating parameters. Even small changes in fuel properties, geometric boundary conditions as well as temperature differences, among other things, can cause previously inconspicuous furnaces to suddenly tend toward undesirable instabilities.
The problem becomes more complex in industrial multi-burner systems where multiple flames interact with each other and the environment. In the future, it is expected that higher proportions of gases from renewable sources will be injected into the natural gas grid in fluctuating proportions for use in industrial thermoprocessing systems. Hydrogen from power-to-gas technologies or climate-neutral generation processes will play a crucial role.
The changes in the main energy carrier for current industrial combustion plants have an impact on combustion properties such as a higher burning speed and thus the flame dimensions as well as the specific exhaust gas volume. The resulting changes in flame behavior pose a challenge to both plant operators and flame monitoring sensor manufacturers. Although real-time measurements, flame monitoring and matched burner control are state of the art for fuels such as natural gas, coal and oil, reliable flame detection and monitoring of natural gas-hydrogen flames are still the subject of research. Detection of hydrogen and mixed flames is challenging because hydrogen burns with a nearly invisible to pale blue flame.
Objectives of the project
Therefore, the objectives of the project are the optimization and development of a new flame monitoring device – thermoacoustic sensor – for use with hydrogen containing gas and for the control of burner systems in connection with thermoacoustic problems as well as for combustion optimization. Furthermore, basic knowledge for innovative systems for the prevention and detection of unfavorable operating conditions in industrial furnaces is to be created.
Work tasks OWI
- Evaluation of the capability of sensors available on the market for the detection of natural gas-hydrogen flames under different conditions in the laboratory
- Development of sensor principles capable of detecting unstable and suboptimal flame behavior at different operating points, in particular under the influence of hydrogen admixture on flame behavior using the example of an industrial burner
- Transfer of sensor principles and signal processing methods to industrial burners
- Numerical modeling of the experimental setup using CFD/ CAA
- Technical evaluation and preparation of the test results for utilization by an industrial partner
Performing research centers
- OWI Science for Fuels gGmbH
- Chair of Gas and Heat Technology at the Institute of Thermal Engineering of the Technische Universität Bergakademie Freiberg
Project funding
The IGF project The 22736 BG / 1 „Thermoakustische Sensorik für Erdgas-Wasserstoff-Flammen im Ofen“ (Thermoacoustic sensor technology for natural gas-hydrogen flames in furnace construction) of the Forschungsvereinigung Forschungskuratorium Maschinenbau e. V. – FKM, Lyoner Straße 18, 60528 Frankfurt am Main is funded via the AIF within the framework of the Program for the Promotion of Industrial Community Research (IGF) of the Federal Ministry of Economics and Climate Action on the basis of a resolution of the German Bundestag.
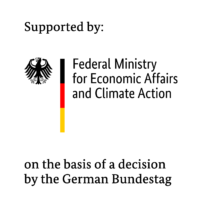
Project durance
01/ 2023 until 06/ 2025
Contact
Dipl.-Ing. Dagmar Kuckelberg
phone: 02407/ 9518-174
email: D.Kuckelberg@owi-aachen.de